- Craft + Main Cabinetry hand selects the finest North American lumber.
- The first layer of primer is applied and properly cured in a high temperature oven. Surfaces are then meticulously hand sanded in preparation for finishing. Dust particles are blown, brushed, and wiped away by hand.
- The second layer of primer is applied and properly cured. The surface is then hand sanded, and dust particles are removed with careful attention.
- The first layer of paint sealer is applied and properly cured. Again, the surface is hand sanded and is cleared of all remaining dust particles.
- The second layer of paint sealer is applied and properly cured in a high temperature oven.
- When a Brush premium finish is selected:
- A wood block is wrapped in sand paper and gently rubbed on the door front to create brush lines on the face of the surface.
- A full wipe glaze is applied to fill the brush lines. Excess glaze is wiped away, and the remaining glaze is properly cured.
- The first layer of AC sealer is applied, and then properly cured.
- When a full wipe glaze or highlight premium finish is selected:
- The chosen glaze is carefully wiped over the door. Excess glaze is wiped away, and the remaining glaze is cured.
- Surfaces are then meticulously hand sanded in preparation for the final top coat. Dust particles are blown, brushed, and wiped away by hand.
- The final layer AC top coat with UV inhibitors is sprayed on by hand, and then properly cured in a high temperature oven.
- The product is continuously monitored for quality and inspected for finish consistency. Gloss levels are checked using a sheen meter.
- Product arrives at the final stages of manufacturing by way of overhead lines and staging carts, providing the most protection possible.
Enamel Finishing Process
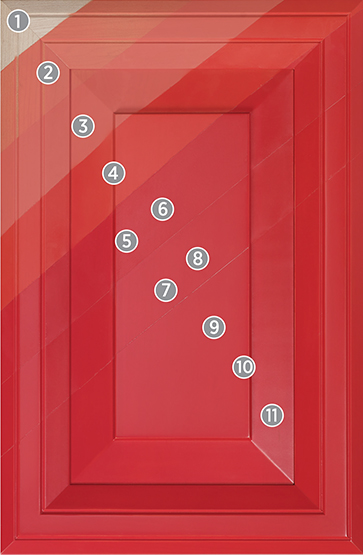
Stain Finishing Process
- Craft + Main Cabinetry hand selects the finest North American lumber.
- All surfaces are meticulously hand sanded with fine grit sand paper to provide the ideal canvas for the finishing process.
- Dust particles are blown, brushed and wiped by hand from the surface prior to each step of the finish process.
- Depending on stain color, we utilize a specially formulated, two or three step color process to achieve the final color. First, a no wipe hand sprayed grain-enhancing dye stain is applied to enhance the natural characteristics of the wood.
- A no wipe hand sprayed pigmented stain is applied to soften and add a rich feel to the first stain coat.
- Depending on final stain color, a third no wipe hand sprayed pigmented stain may be applied to complete the color process.
- Product is then oven dried at specific times and temperatures before moving on to the first sealer coat.
- An environmentally conscious AC sealer is hand sprayed, then properly cured in a high temperature oven.
- Product is seal sanded by hand in preparation for a second sealer coat.
- A second coat of AC sealer is hand sprayed, then properly cured in a high temperature oven.
- Product is seal sanded by hand a second time in preparation for a top coat.
- A third dense coat of AC top coat with UV inhibitors is sprayed on by hand, then properly cured in a high temperature oven, providing a durable finish and pulling all the color from the multi step color process to the surface.
- The product is continuously monitored for quality and inspected for finish consistency. Gloss levels are checked using a sheen meter.
- Product arrives at the final stages of manufacturing by way of overhead lines and staging carts, providing the most protection possible.
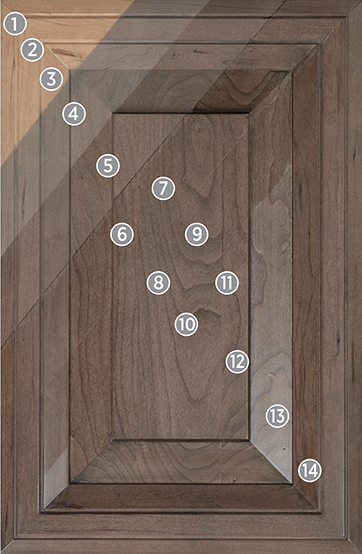